Chapter 10: Harvesting
Chapter 10 – PDF version
Download the PDF version of ‘Chapter 10: Harvesting’.
When producers are evaluating flax harvesting systems, a number of factors should be considered including:
- existing equipment inventory of combine(s), header(s), windrower(s), and straw collection;
- residue management requirements;
- harvest system placement within an overall agronomic plan; and
- potential straw management for collection and fibre recovery;
Straight combining has generally become a preferred method of harvest for all Prairie crops wherever possible due, in part, to the availability of large, sophisticated headers, improvements in maturity uniformity of varieties, reduced labour and equipment inventory cost, and harvest time reduction.
Conventional Straight Combining
Flax harvesting can be accommodated within a straight combining system but its harvest may offer unique challenges and opportunities related to the tough, fibrous nature of the straw. Cutter‐bar style headers can be used provided the sickle bar is in good condition and the flax straw is mature and dry. Cutter bars of combines or windrowers must be kept clean and sharp to ensure a smooth cut and to prevent accumulation of immature flax straw under the knife. Consult your local dealer or machine manual for recommendations regarding sickle knife designs that are best suited for cutting flax. Desiccation of the crop to force straw dry-down and reduce harvesting issues associated with weeds and immature straw could be considered as an alternative to waiting until the crop naturally matures or until a significant frost event improves the potential to cut the straw. Dry, mature straw and seed is essential if the combine is to properly separate the material without excessive seed or seed quality loss. However, either desiccation or waiting can impose economic risk due the cost of the spraying operation, crop trampling, or losses due to wind or rain.
Production Tip
Harvest the crop at the appropriate stage of maturity. Flax is considered to be fully mature when 75% of the bolls have turned brown.
Alternative Straight Combining
In plot and field scale studies conducted from 2006 until 2012, Agriculture and Agri-Food Canada (AAFC) compared the use of conventional straight combining to the use of a Shelbourne-Reynolds stripper header. This stripper header has a counter-rotating rotor containing stainless steel stripping fingers that strip seed from the crop as the combine moves the header forward in the field. After the grain has been stripped by the rotor, the grain and chaff are deflected back into a conventional auger and pan. The majority of the crop’s straw is left standing in the field attached to the soil, reducing substantially the material entering the combine and leaving the straw relatively untouched and available for future collection or soil protection. For a more detailed description of this header, see:
http://www.shelbourne.com/3/products/1/harvesting/31_stripper-header.
The results of demonstration scale field trials have shown that the use of the stripper header offers a number of opportunities and challenges when used in flax:
- Since much of the seed is threshed by the header and little straw is introduced into a combine, combine separation and harvest capacity can be improved or combine size reduced for a given header width.
- In demonstration trials conducted in 2007, flax seeded around May 1st was harvested by a rotary combine/stripper header as early as August 16th , when the seed was mature and dry and the straw still green. This reduced harvest risks associated with weather and time, eliminated the need for desiccation, and allowed the flax straw to rebound from being trampled making it available for collection. Normal harvesting with a conventional auger and a draper header occurred approximately six weeks later when the straw had matured and dried adequately.
- Stripper header rotor speed was increased over recommended to accommodate higher forward combine ground speed.
- The bull nose deflector needed to be positioned so that the bottom of the deflector was placed only a minimal amount into the crop canopy. This was especially critical in desiccated flax crops where embattlement of the standing crop was observed. A visual indicator placed on the bull nose assisted the operator to determine the correct deflector setting for the crop being harvested.
- The rotor height setting needed to be as low as practical and gauge wheels were added to assist the operator make this adjustment.
- Overall flax seed and straw recovery comparisons for the Simonson Farms Ltd. demonstration trials are contained in Table 10-1. No statistical significance can be derived due to the small number of samples, locations, and years involved in the trial.
- Recoverable fibre based upon hammer-mill fibre extraction technology showed that straw from stripper header harvesting had a 9% improvement in cellulose recovery over other harvest methods.
Yield Comparison
2005 to 2008 Simonson Farms Ltd. |
Average Grain Yield
(Kg/ha) |
Grain Yield
% of Draper Header |
Average Straw Yield
(Kg/ha) |
Straw Yield
% of Conventional Draper Header |
Stripper header: Massey and Case IH combine data | 1144 | 98 | 794 | 132 |
Auger header and Massey Combine | 1253 | 108 | 783 | 130 |
Draper header and
Case IH combine |
1166 | 100 | 603 | 100 |
Table 10-1. Plot trials from 2008 to 2011 using the same Massey conventional combine compared a Shelbourne-Reynolds stripper header to a conventional Massey auger header at Indian Head and Swift Current, Saskatchewan. Seed recovery was lower for the stripper header (6.5% lower at P=0.002) but straw recovery trended higher. This seed loss was verified to be predominately header loss through ground surface evaluations following harvest operations.
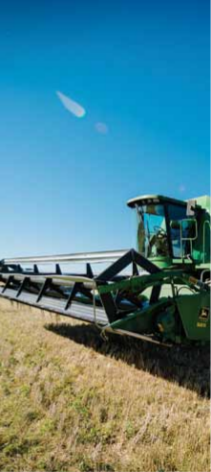
Production Tip
Avoid cracking the seed during harvest by using correct combine adjustments.
Swathing
Flax is considered to be fully mature when 75% of the bolls have turned brown and swathing can be considered at this stage. Cutting or desiccating flax at an immature stage is not known to result in seed blackening, but yields will be reduced due to early termination of seed development. This will result in thin seeds of lower weight.
If re-growth occurs in the fall, cut the crop when the greatest amount of ripe seed can be obtained or consider desiccation at this time. Fall rains may cause weathering of the mature seed and frost may cause immature seed to turn black, resulting in grade reduction. Considerable frost damage occurs in immature seeds when temperatures drop to the -3o to -5oC range (27o to 23oF), while leaves are severely damaged at -4o to -5oC (25o to 23oF) and stems at -6o to -7oC (21o to 19oF).
When swathing, a stubble height of about 10 to 15 cm (4 to 6 in.) is recommended to hold the swaths off the ground and facilitate drying. Flax swaths can be rolled to prevent movement of the swath by strong winds.
Chemical Desiccation
Chemical desiccation may be used to accelerate drying of the crop and any weeds that may be present. It does not speed crop maturity, but will reduce the time from maturity to harvest.
Potential advantages from this practice are:
- earlier harvesting;
- elimination of the need for swathing;
- reduction in combining time;
- less wear and tear on machinery;
- cleaner seed;
- weed control; and
- reduction or elimination of the need for artificial drying.
A desiccant may be applied when 75% of the bolls have turned brown, which is the normal time of swathing. Generally, application of approved chemicals 7 to 14 days before the target harvest date should ensure best weed control and maximize harvest management benefits. Thorough weed dry down usually occurs in 10 to 14 days following application. Desiccated flax should be harvested as soon as possible after it is suited for cutting and threshing, to avoid capsule loss and weathering of the seed. For up-to-date information on the use and application of chemical desiccants, refer to the latest provincial recommendations or consult your local agronomist or provincial agricultural Agrologist.
Market News
Linseed oil is well‐regarded as an excellent preservative for wood and concrete surfaces.
Threshing
The combine must be adjusted correctly to minimize seed coat damage to flax and minimize unwanted losses due to the header operation or threshing. If seed is excessively dry, it becomes more susceptible to damage from high threshing cylinder speeds or tight concave clearances. When a stripper header is used, the material being separated by the combine is missing much of the straw and the opportunity exists for increased seed and chaff intake. Many of the settings of the combine must change, including cylinder speed, concave clearance, fan speed/separator airflow, and sieve opening. If the seed is to be used for planting, greater care in threshing is required as seed with a damaged seed coat has reduced germination. It may be necessary to adjust the combine from time to time during the day depending on temperature, relative humidity and the condition of the flax. The manual provided with the combine should be consulted for correct settings and recommended adjustments for specific conditions or observations. Usually, early-sown flax is easier to thresh than late-sown flax because it has a better chance to mature under drier conditions.
The swath may be threshed when the leaves and stems are dry enough to separate in the combine and the seeds rattle in the boll, or when the seed has dried to the desired moisture level as indicated by a moisture meter.
Delayed combining of flax may result in weathered seed. Weathered seed often has a grey, dull cast and may turn black. Another risk of delayed harvesting is boll drop, where bolls break off the ripe plant and fall to the ground.
Flax is considered tough from 10.1 to 13.5% moisture and damp if over 13.5% moisture. Although flax seed is generally considered dry enough for storage at 10% seed moisture content, the crop may be harvested at higher seed moisture if drying facilities are available. For further information, refer to the Flax Storage section.
Although many recent combine models offer options to improve residue quality available for baling in general, flax fibre recovery of the highest quality may still be compromised. Producers who are planning to collect straw while using conventional headers with their combines should consult combine manuals, dealers, or internet resources to determine the best operational practises for their specific equipment.
Residue Management
Where flax residues are to be managed in the field, the combine, header, and residue disposal options are similar to those for cereals. Combine designs released by manufacturers over the past decade have considerable engine power and residue chopping/spreading capacity available to distribute chopped flax residue across the crop cutting width. Additionally, chemical desiccation or especially pre-harvest application of glyphosate, tends to make the straw more brittle and hence easier to chop and spread. Recent combine improvements and desiccation may reduce or eliminate the need for other residue management operations but may slow harvest due to the power needed for residue size reduction and spreading. If adequate residue treatment is not achieved, other residue treatment options should be considered to prevent issues with subsequent field operations.
Straw disposal by burning can be used to significantly reduce flax residue. A “straw buncher” has been developed to collect windrowed flax straw into piles that can be more easily and completely burned in the field (Figure 10-1). However, if the straw is removed by burning or baling, soil may become more vulnerable to erosion if summerfallow succeeds flax. Therefore, a cereal crop following flax is required to rebuild crop residues or continuous cropping should be used with a cereal as the next crop. Recent research has shown that none of the residue management methods appear to affect the yield of a succeeding crop of wheat.
Baled mature flax straw can be used for ruminant animal feed or animal bedding. However, green flax straw should not be fed or grazed as it is high in prussic acid. The danger of prussic acid poisoning is much higher if the immature flax is frozen.
Flax straw may contain between 10 and 22% fibre and represents a strong natural fibre of interest to the industrial sector for uses such as fibreglass replacement, composite plastic parts manufacturing, specialty paper production, and insulation. If producers wish to consider straw as part of their economic return from flax production, the complexity of flax harvest management for producers increases because straw quality, collection system type, and operation integration all may affect end use suitability, producer costs, and market returns. Fibre length and the quality of fibre retting are influenced by harvest system and variety. In trials conducted by AAFC, Biolin and SWM International, different options to increase retting and improve processing of flax straw were evaluated based upon flax straw remaining behind a stripper header. These included a number of conditioning, cutting, and packing operations designed to improve opportunities for retting bacteria and fungi to attack and partially decompose the flax straw in the time available following seed harvest. The straw was left in the field until spring and collected two weeks prior to when normal agronomic operations would commence for the specific location, with the results compared against standing flax straw overwintered then swathed and baled.
Production scale testing of spring baled winter retted flax produced cleaner, lower shive content, improved fibre length and fibre strength, than traditionally baled fall straw. Spring retted straw materially improved processor returns by increasing production rates, yields, and quality of fibre while reducing shive content level. The resulting fibre product had improved marketability characteristics for higher value applications.
The use of a forage macerator (super conditioner), while not showing improvements in retting success, showed promise as a bale densification device. In a demonstration scale evaluation, 180 cm (6′) round bales of untreated straw weighed ~ 670 kg (1350 lbs) while 180 cm (6′) bales of macerated straw weighed ~1000 kg (2200 lbs). This represented an improvement in bale density greater than 50%, allowing road transport to achieve or exceed legal load limits when macerated bales are the payload. This reduced transportation cost and provided more fibre per bale with potentially positive benefits for storage and processing for the fibre processor.
Flax Storage
Dockage can be reduced by controlling broadleaf weeds as well as grassy weeds, including volunteer cereals, during the growing season or through pre-harvest desiccation. If green weed seeds are present, they may raise the moisture of the flax seeds enough to cause heating and moulding. Removing this dockage before putting the flax into long-term storage is advisable. Freshly harvested seed can maintain a high respiration rate for up to six weeks before becoming dormant. As in other oilseeds and cereal grains, moisture migration will occur in stored flax seed. Even though the seed is binned with uniform moisture, high moisture spots can develop by moisture migration. This usually happens in fall and early winter, although it can also occur in the spring. This, coupled with mould growth can lead to heating. In general, stored flax requires more attention than stored cereals, so bins of flax seed should be inspected frequently for problem spots until the seed has cooled down. Whenever possible, it is recommended that flax seed should be cooled down after it is put into storage. See Figure 10-2 for more information.
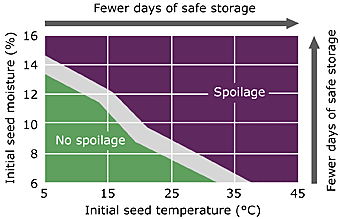
Storage insects
Stored flax seed is not troubled by storage insects as frequently as cereal grains. This may be because flax does not provide a nutritionally optimal diet for many insects, mainly because of its high lipid and low carbohydrate composition. Insects that can occur in stored flax are the saw-toothed grain beetle, confused flour beetle, merchant grain beetle, and red flour beetle. Various fungus beetles and numerous mites can be found in seed that remains tough to damp in storage. Research in Manitoba has revealed that flax varieties vary in their susceptibility to the saw-toothed grain beetle.
The rusty grain beetle occurs occasionally in car lots of flax. However, it is suspected that this insect feeds on cereal admixtures in the flax. Research in Manitoba found that rusty grain beetles were not able to reproduce or complete development on flax. Granary weevils and rice weevils exposed to whole flaxseed all died.
The optimum temperature for rapid growth of insects is in the range of 30° to 35°C (86° to 95°F). Their activity is greatly retarded by temperature below 18°C (64°F). If the grain is cool and dry, insects will generally not thrive. However, flax may be put into storage at an acceptable moisture content and temperature, but pockets of high moisture and temperature can develop later through moisture movement on convection currents and heat production by mould respiration which would encourage insect activity.